Mercy Hospital & Medical Center
Case Study
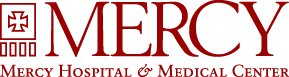
Overview
Mercy Hospital and Medical Center, Chicago’s first teaching hospital, had served the city since 1852. With 479 licensed beds and more than 350,000 outpatient visits a year (2011), Mercy was a Level II trauma center complete with a comprehensive network and teaching affiliations with the University of Chicago and the University of Illinois at Chicago.
In its century and a half of serving Chicago, Mercy was a pioneer in health care and its commitment to helping patients. The hospital continuously evaluated its operating expenses, including supply chain strategies, to determine where it could decrease costs and reallocate resources to ensure clinicians had the tools to do their job and increase patient focus. When the hospital began experiencing a high amount of dissatisfaction from clinicians running out of supplies and doctors foraging for supplies, Rick Cerceo, Executive Vice President and Chief Operating Officer of Mercy at the time, knew a change needed to happen.
Identifying the Right Solution
Rick and his team began with incremental supply chain improvements. Still, they quickly realized that Mercy needed an end-to-end solution that could dramatically reduce costs and allow clinicians to focus on providing quality care and addressing patient needs rather than managing supplies. These needs led them to BlueBin.
BlueBin’s Kanban solution was exactly what we were looking for.
“BlueBin’s demand flow (Kanban) solution was exactly what we were looking for,” said Rick. “Its low-tech approach coupled with robust software and lean management techniques brought bottom-line savings to the hospital and genuinely helped us continue our mission for our patients.”
After hearing Charles Hodge, Founder and CEO of BlueBin, speak at a medical supplies distributor conference, Mercy asked Charles to help implement BlueBin’s solution and assist the hospital in its lean journey. In his presentation, Charles highlighted BlueBin’s demand flow method, based on a 2-bin Kanban system that creates visual cues or signals – in this case, to indicate the need to replenish supplies. The Kanban system provides immediate, tangible, and measurable changes toward lean methodology. These features resonated with Rick.
“In the auto industry, lean manufacturing makes sense, and you can visualize how it works. Although we were already learning about and implementing lean manufacturing techniques, it was difficult to conceptualize how it could work in health care. BlueBin helped us put these techniques into practical uses and gave us the right application with the right tools,” Rick said.
Deploying BlueBin
In July 2011, Mercy began implementing BlueBin’s solution to help save time and money, develop a unified, data-driven supply chain operation, and introduce and sustain standard work and lean processes that drive continuous improvement. The organization deployed BlueBin’s visually-managed 2-Bin Kanban system, which focused on the total cost of ownership and waste elimination.
The process is simple. Mercy stocks supply areas with two bins for a particular product. The front bin holds a specified level of supplies, and when that bin is empty, clinicians can immediately access the second bin. All that is asked of the nurses is to place the first bin on the top shelf when they use the last item and then pull the second bin to the front. Replenishment is triggered when someone puts the empty bin in the designated holding area. Before emptying the second bin, supplies are reordered for the first, restocked, and replaced in the supply area.
Our staff was running out of supplies, which delayed procedures and patient care.
“Before we implemented BlueBin’s solutions, our storerooms were overused and we weren’t centralizing the purchase of supplies. Our staff was running out of supplies, which delayed procedures and patient care,” said Rick. “This forced nurses to start ordering their own supplies, and supply rooms began bulging at the seams because they were so afraid of running out. Now I can say these problems are completely gone, and the process has been amazing. Nurses and doctors are very busy and have so many demands. Managing supplies shouldn’t be one of them.”
In addition to the Kanban program, BlueBin provides analytics software (BlueQ Analytics) that allows Mercy to see which supplies are used by unit, seasonally, and how quickly they are consumed. BlueQ Analytics provides the hospital with actionable insights and real-time monitoring to predict when the hospital will run out of supplies before it happens.
We now have one standard process that ensures everyone in the hospital has what they need, when they need it.
“Now, nurses don’t have to order anything; it’s all done for them and takes the burden off management. Ordering is automated and done electronically based on the lowest unit of measure,” Rick said. “Where we once had different processes for managing supplies throughout the hospital (the OR did its own ordering, the lab did its ordering, etc.), we now have one standard process that ensures everyone in the hospital has what they need, when they need it.”
What About the Results?
BlueBin specializes in lean supply chain solutions for healthcare organizations and has perfected this approach which was never before thought possible in healthcare. Most customers experience ROI within 12 months of implementation.
Since implementing BlueBin’s program, Mercy has saved more than $1 million a year in waste and excess supplies, more than 28,000 clinical hours previously spent foraging for supplies, and has reduced its bulk storage space by nearly 50 percent. Additionally, the intuitive BlueBin Kanban system has increased productivity for supply technicians or material handlers who replenish supplies, saving labor hours equivalent to four full-time employees.
BlueBin helped us give them more time at the patient’s bedside, and as a result, we’ve seen a positive impact in patient satisfaction.
“We used to get nearly 100 calls a day from staff who were looking for supplies. Now, post-implementation, we get less than 100 in a month,” Cerceo said. “Our clinicians no longer need to spend their valuable time managing supplies. BlueBin helped us give them more time at the patient’s bedside, and as a result, we’ve seen a positive impact in patient satisfaction.”
Soon after deploying BlueBin, Jelena Marinkovich, Mercy’s Director of Supply Chain, surveyed the nursing staff to determine their level of satisfaction and whether the Kanban system has improved their day-to-day duties. The proof is in the results: 99 percent of nurses said it was much better than Mercy’s previous supply chain process. Marinkovich believes that the other one percent are nurses who had yet to implement the Kanban technique on their floors.
“The neat thing about the 2-Bin Kanban system is that the nursing staff is involved in deciding what supplies are needed, where they want them laid out, and how to place items next to other items. It’s very intuitive, and they have ownership in it. This isn’t our program anymore. It’s theirs,” said Rick.
Mercy believes its savings will continue to increase. However, beyond waste reduction and cost savings, the organization believes that BlueBin has helped the hospital focus on what matters most—patient care.
Ready To Get Started?
Contact us today to discuss your our 2-Bin Kanban systems and supply chain analtyics for healthcare!